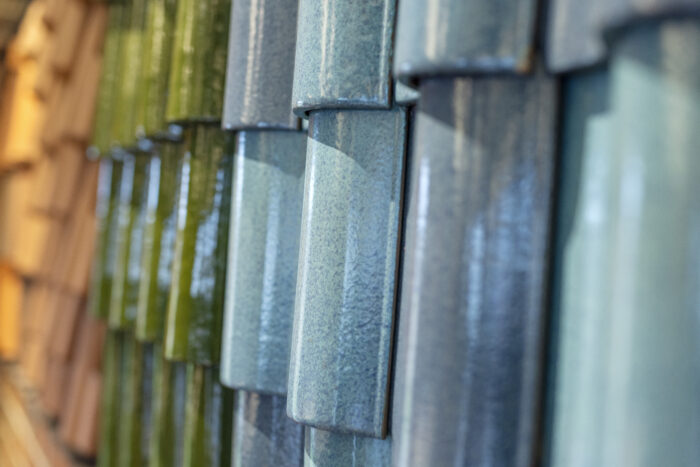
When it comes to sustainable building materials, terra-cotta is at the top of the list.
Made from the earth’s clay, terra-cotta is natural and inherently free of dangerous chemicals. It can be used for roofing, cladding, interior surfaces, and more. And with a lifespan upwards of 75 years, terra-cotta’s extreme durability across applications and climates is a natural deterrent against throwaway culture.
Green Build & Design Magazine talked to terra-cotta expert David Jensen, sample coordinator, glaze production scheduler, and color consultant at architectural terra-cotta manufacturer Ludowici about what makes terra-cotta so durable. Here he sets the record straight.
Breaking Down the Durability of Terra-Cotta
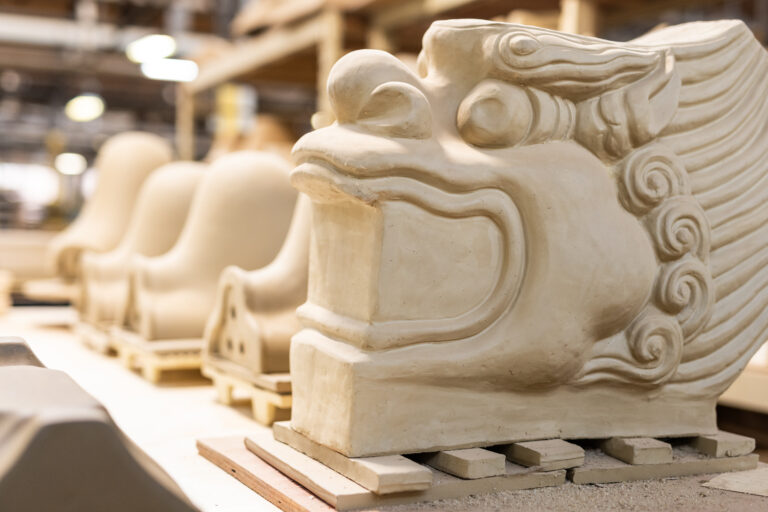
“It’s a common misconception that glazing is what provides waterproofing to terra-cotta tile,” Jensen says. “In actuality the biggest impact for durability comes from the clay body itself.”
Clay can be a porous material, which means it can absorb water. If the clay has a high porosity then water will seep into any pores within that clay body. In buildings that’s where problems can arise.
“If water seeps into pores of a weak clay body and then freezes it’s going to expand, which will put tension within that clay body,” Jensen says. “It may not crack it immediately, but it’ll induce stress within the clay. Over time, if that water keeps freezing and melting and freezing and melting, it’s going to keep putting pressure on it until eventually that clay is going to crash.”
That’s why Ludowici puts an emphasis on the clay body in all of its terra-cotta tile products.
“We make our clay body dense enough that it doesn’t soak up water in the first place,” Jensen says. “That’s something we take pride in because even though it may not be the most glamorous aspect of the tile, the clay body is really what lets our product last as long as it does in so many different environments.”
Ludowici’s clay body is mined locally and run through filters to ensure quality. Once mixed and turned into actual clay, it’s then fired at a high temperature to fully vitrify the clay without causing it to warp or decay.
“It’s a tricky balance,” Jensen says. “At other companies it can be common to play it safe and fire the clay at a lower temperature. But the downside is that it makes it more likely that the clay will absorb water and be less durable over time.”
Ludowici’s process, however, has been perfected over the company’s 135 years in business. The final terra-cotta tiles undergo absorption and break-strength testing to ensure the durability and quality they’ve been known for since 1888.
“Oftentimes you’ll see roof tiles that Ludowici made well over 100 years ago come back here for a restoration project that we’re trying to match,” Jensen says. “When we say terra-cotta tile lasts, it’s not just a guess. It’s something we know pretty well.”
The Green Benefit of Terra-Cotta Glazing
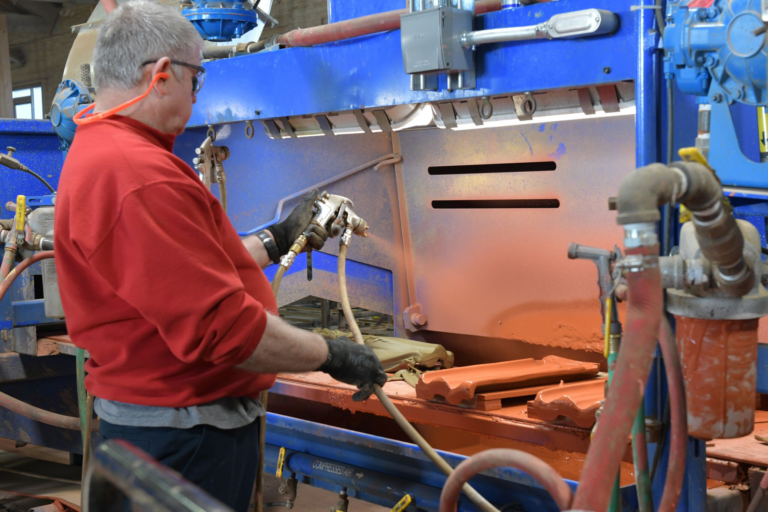
Even though glazing may not add to terra-cotta tile’s durability and weather-resilient properties, it does add another sustainable benefit to the already green material: a high solar reflective index, or SRI value.
“A high SRI value means that a building is reflecting more light, so it’s not absorbing or trapping much heat. It’s releasing most of the heat that’s reflecting on it,” Jensen says.
Glazing terra-cotta tiles in certain colors can help boost a building’s SRI value, but it can be a challenge depending on the aesthetic direction of a project.
“Matte white, for example, has the biggest SRI value, but something like a matte black will have a lower SRI just because black is more likely to trap heat,” he says. “It’s really a combination of aesthetics and how climate-friendly you want a building to be. It can be difficult if you’re trying to balance the aesthetics with a desired SRI, but that’s partially just the nature of working with color.”
At the end of the day terra-cotta’s durability comes down to a solid clay body, low porosity, and high breaking strength. Glazing that increases a terra-cotta’s SRI value is an add-on to the already green material.
“The fact that we make a product that doesn’t have any harmful chemical byproducts is always a great comfort to me,” Jensen says. “It’s clay that comes from the earth, and it can go back to the earth.” Eventually, that is. In about 100 years or so.
Sophia is a Chicago-based writer and editor. With a background at both agencies and print publications, her writing ranges from the built environment and manufacturing to health and travel.